GreatPlaces Housing Group (GPHG) is a profit-for-purpose organisation in the North-west that gives back to our customers, communities and colleagues. Providing general needs rented homes and tenancy services. As well as accommodation and services that promote independence and wellbeing for some of society’s most vulnerable people since .
The Challenge
Our mission was to improve the current internal heating systems throughout 100 properties across Great Manchester. The primary requirement was to replace the more traditional use of tank fed hot water systems which were corroding on the inside, causing contamination as they had not been updated for many years. Another issue was the positioning of the tanks inside the property; most are situated at the entrance of the property, with concrete floors surrounding them. This location made it very difficult to reach and remove the pressure release valve.
We had to complete all this work whilst ensuring compliance with both Building and Water Regulations. Although different Regulations, which are mutually exclusive in regard to installations, application of both can contradict the other, making it challenging to ensure compliance with both.
The Solution
Due to the size of the contract, Great Places Housing Group provided us with a specification for the installation. This specification consisted of unvented cylinders, however, following an initial inspection of the properties, we identified that this would not be a viable solution. Using this option, it would have been impossible to install the discharge pipework to comply with G3 of the Building Regulations, necessary for the unvented option.
Therefore, a thermal store was required, one with the ability to provide mains pressure hot water and without the requirement for discharge pipework or on-going annual maintenance. We delivered the solution: providing bespoke-sized McDonald’s cylinders. In order to combat the positioning issues we installed CUBEflow tanks which took up 27% less space within the cupboard and which were designed to fit the available space. As a result, this also created some extra storage space for the residents.
The Results
The results of this work meant in a better quality heating system for all the residents involved, thus a further saving for them and the clients, which during the current financial climate is quite the positive. Furthermore, the thermal stores’ ability to generate the mains pressure hot water, by passing the mains cold water through the highly efficient internal coil. This ultimately means the hot water is produced instantaneously and not stored, therefore zero risk of legionella.
Conclusion
In conclusion, the use of the CUBEflow tanks proved to be a great solution to suit this project. This allowed us to eliminate the conflict between the Building and Water regulations, whilst also being designed and manufactured to suit the available space within the property. Our solution, derived by the M&R team and the McDonald’s water storage representatives, allowed for a seamless change in heating systems and en-sured that all residents were satisfied with the works completed, and the most common response to the works was that they were able to use the additional storage space created by using bespoke sized cylinders.
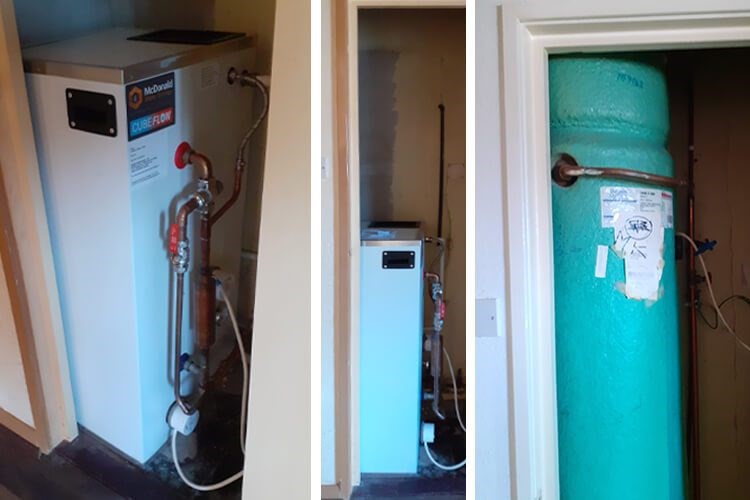